Case
Extreme stable unguyed mobile mast
- Client:Military Northern Europe
The Objective: Design, Develop, Manufacture and Assemble an ultra-high unguyed mobile telescopic 45m mast.
GEMCO develops and manufactures Special Vehicles and Shelters i.e. for Tactical and Critical Communication Support. Most of these units are equipped with a 30m telescopic mast that require guy wires for stability.
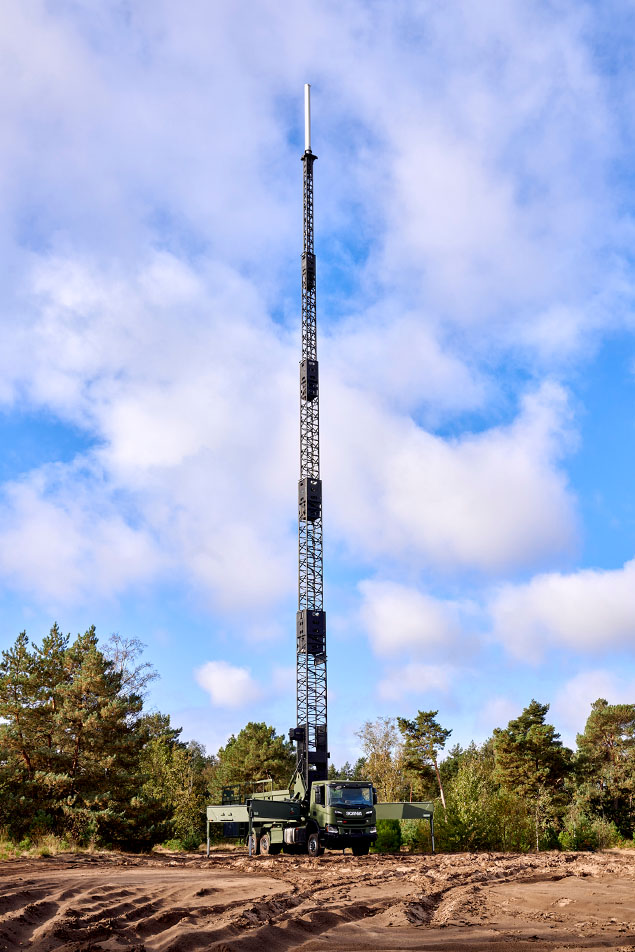
The case
We were challenged to develop and build an extreme stable unguyed mobile mast with a height of 45m. For use in harsh densely wooded forest environments in Northern Europe. The mast must be able to carry a minimum top load of 200 kg, it must operate in a temperature range of -40°C to +45°C, provide stability of max. 2° @ wind load of 30 m/s, and it must be climbable as well.
“Extending the height from 30m to 45m.”
The challenge was to go from 30 meters to 45 meters. The current operating principle of the mast was not scalable to such heights. There were risks in achieving insufficient stability within the permissible weights of the truck.
- Stiffness
- Erection of the mast
- Ice buildup
Technical challenges/ bottlenecks
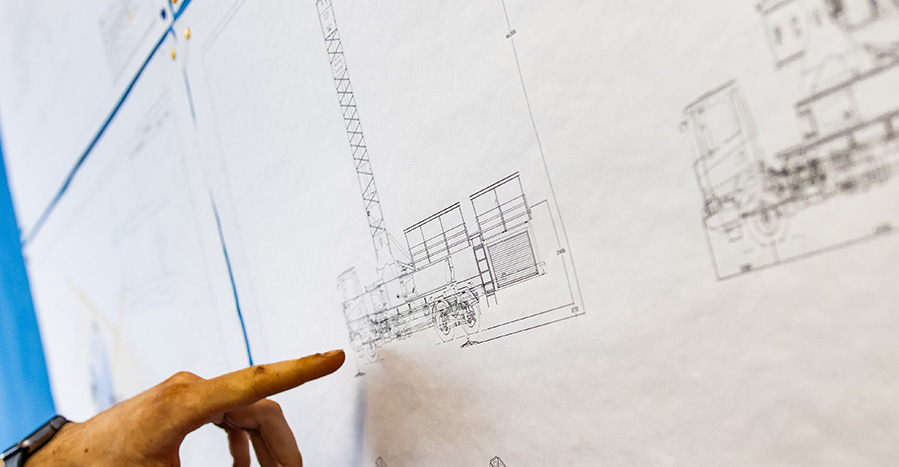
Challenges
A/ Stiffness; the 5 square truss segments are erected via a telescopic construction. Each section is quadratic sensitive to buckling.
To meet the stiffness requirements a stiffer material than the usual aluminium must be used, or much more material must be used. However, both options are impossible due to the maximum permissible weight of the truck. In addition, the stiffness requirements for the mast are extremely high in this case, since the mast must be unguyed.
B/ Erection of the mast; the mast, which is horizontal on the truck in transport mode, must be able to tilt vertically at the rear of the truck in our standard vehicle configurations. However, the 45 meter mast will be too heavy to move the center of gravity behind the truck without the front rearing.
C/ Ice buildup; the mast must be operational at very low temperatures even when inevitable ice build-up occurs on the mast and hoisting winch. This increases the diameter of the hoist winch drum, allowing the hoist cable to run off the pulley, Causing the mast to collapse.
The Gemco Answer
“The development and construction of the vehicle took only 7 months.”
TEAM GEMCO
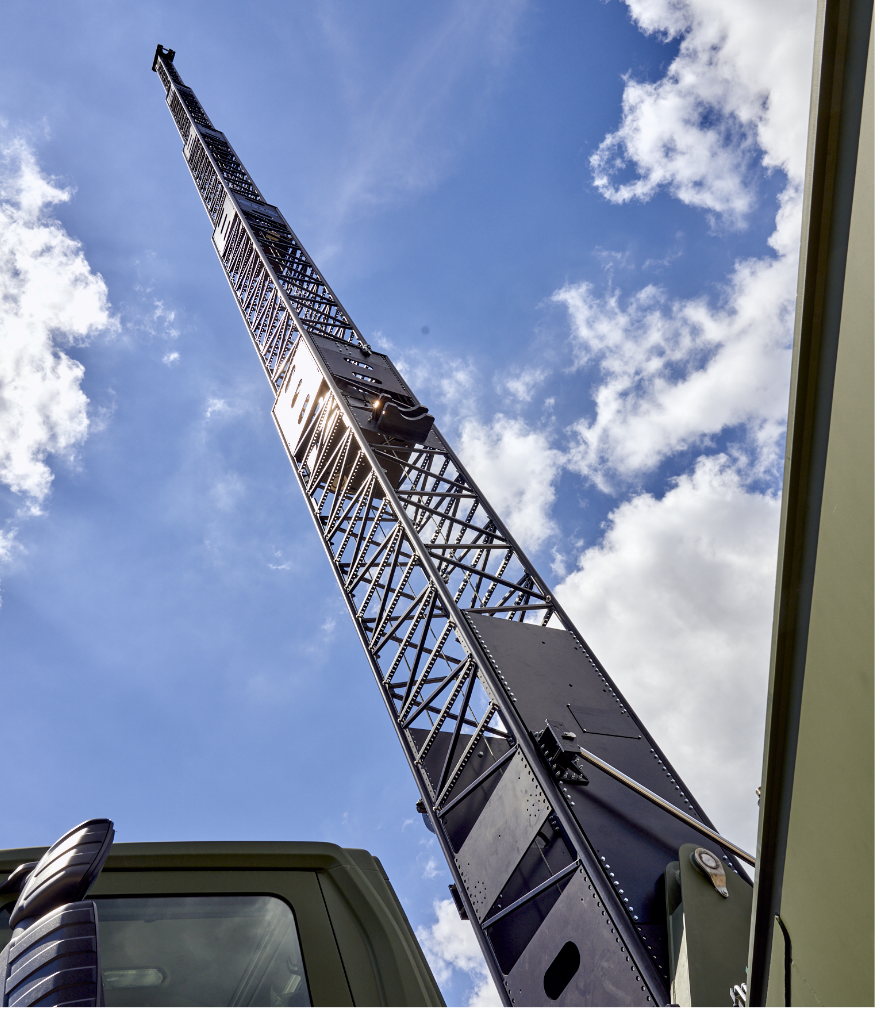
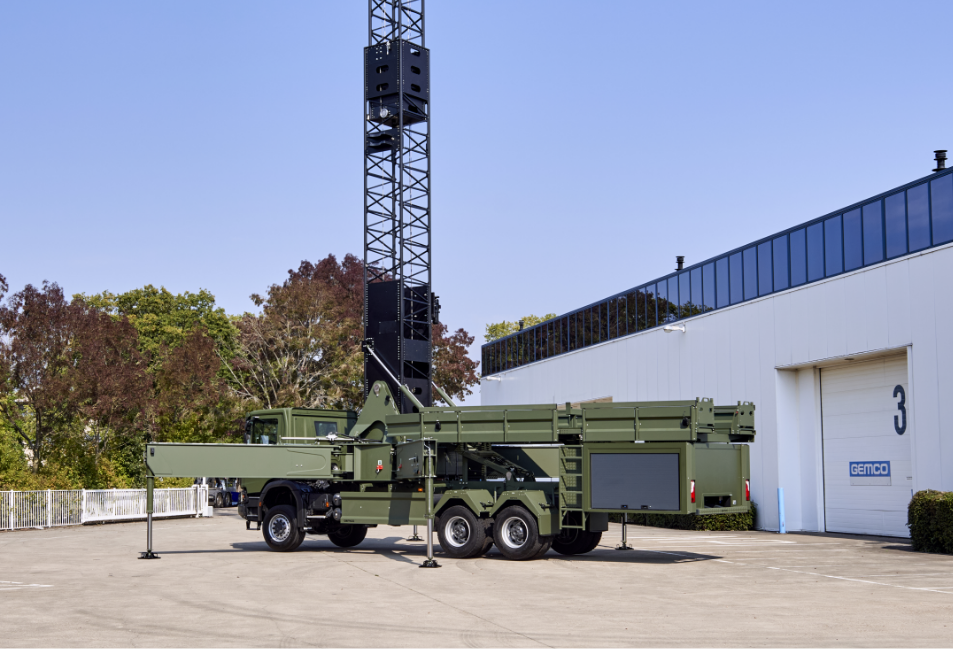
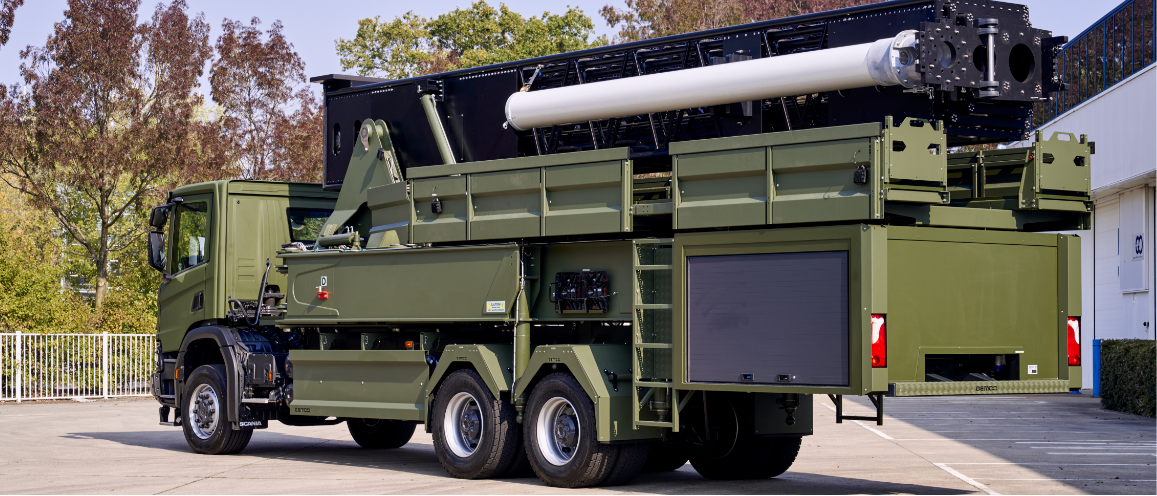
A/ Stiffness: GEMCO has done extensive research and developed a new geometric aluminium profile for mast parts that is much less prone to buckling.
B/ Erection of the mast: GEMCO developed a connection interface on both sides of the truck frame that allows the mast itself to be deployed to obtain rigidity in the construction. The lowest mast segment is used so that a hinge construction can be placed in the middle of the mast construction in a frame part with cross connections.
C/ Ice buildup: GEMCO developed an ice scraper for, among other things, the hoist winch that is guided over the scraper with minimal friction. Avoiding risk of hitting the scraper, which could damage the winch.
GEMCO developed a complete new aluminium light weight mast structure including a Heavy Duty steel connecting frame with support legs for installation and erection/tilting on a truck chassis. The development and construction of the vehicles took only 7 months. Two of these trucks have been built and are successfully deployed by a special military department in Northern Europe.